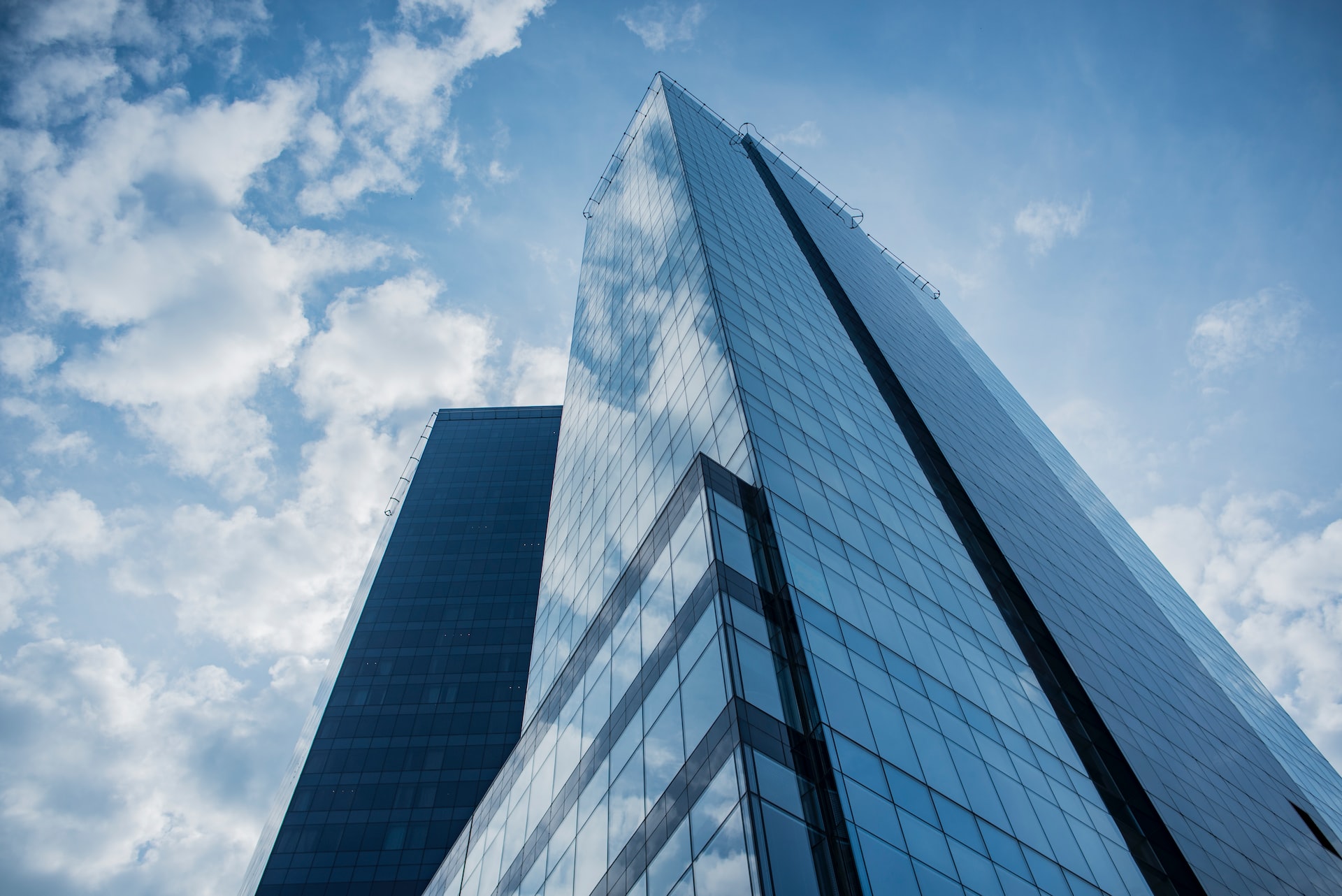
Energy efficiency is the name of the game and commercial buildings are no exception. It’s true that as we learn we grow. Now, we have a greater understanding than ever before of how we produce products for buildings. The recent Inflation Reduction Act included incentives for commercial building energy efficiency. Now, we are prioritizing green buildings in a more aggressive manner. The latest building energy efficiency trends drive that point home.
Making your money count
Gone are the days of the bottom line alone. Building skyscrapers has become more complicated. Now we spend wisely.
When we buy materials, we study their carbon footprint. How much carbon emissions are used to produce that product? To transport that material to the site? How will that material or product perform once it becomes a part of the building? What is required to dispose of this product once it has reached its “end of life” performance?
The building itself is now erected according to its carbon emissions production more than its cost. What choices can be made to further carbon neutrality? Is the HVAC system energy efficient? Are we using a boiler system for heat? It all matters.
There are numerous attributes to analyze when considering the long-term output of carbon from a commercial building. Moreover, carbon emissions taxation is being implemented to ensure compliance. For those property owners who would rather ignore the new legislation, it won’t be so easy moving forward. At some point, you’ll have to step up to bat. Below are the latest trends in energy-efficient buildings to help you get started.
Low embodied carbon building materials
Low embodied carbon is a rather recent term created to describe the carbon emitted through the lifecycle of a particular product or building material. It may surprise you to know that 31% of global carbon emissions come from making things. Therefore, we can conclude that manufacturing materials and products contribute significantly to climate change.
Until recently, priority consideration focused on carbon emissions from operating buildings once they were built. But carbon emitted from the production, transportation, installation, maintenance, and disposal of a building product is also important. These carbon emissions combined provide the true total carbon footprint of a building.
Moving forward low embodied carbon building materials will take precedence in how buildings are created. This may result in more local distribution whenever possible – as a result of the transportation of building materials to the site.
HVAC systems In 2014, data showed that HVAC systems were responsible for up to 35% of the carbon emissions in a typical building. This is a growing concern as there are now greater options for “fueling” an HVAC system. The latest objective is to power HVAC systems via electricity that is generated by a clean energy source, such as the sun or wind.
This is preferable to units that run on natural gas or propane, as these natural fuels require more carbon overall – from excavation to transportation. Transitioning can take time and impact budgets, however, the new Inflation Reduction Act has approved numerous incentives for commercial buildings to implement energy savings.
Tax Incentives for Property Owners
These rebates will benefit commercial property owners as follows:
- Up to $1,600 for insulation, air sealing, and ventilation.
- Up to $1,750 for a heat pump water heater.
- Up to $2,500 for electric wiring.
- Up to $3,000 for solar panel installation
- Up to $4,000 for a breaker box upgrade.
- Up to $8,000 for a heat pump for space heating or cooling.
All of these options will bring a building closer to carbon neutrality. These solutions combined are what create a green building. Now that we have learned the many ways in which a building can produce carbon emissions, we see the opportunities for change and can act accordingly.
With a renewed emphasis on examining and maintaining a building, achieving optimal energy efficiency is more readily obtainable. It’s in understanding how one system may positively or adversely affect another, that allows for true energy savings.
Air quality
Another trend in buildings is clean air systems. Covid brought a greater emphasis to office air circulation and how employees are affected by illnesses due to poor air quality. Currently, we are seeing popularity with upgraded air filters that prevent microorganisms from traveling through the atmosphere.
Currently, the CDC and ASHRAE both provide professional guidelines for buildings regarding air quality. Many manufacturers use the Clean Air Delivery Rate (CADR) system to rate air cleaner performance. Others have implemented High-Efficiency Particulate Air (HEPA) filters. Either way, this may become the standard for new commercial buildings as they are established.
Ultimately, HVAC systems have a substantial impact on carbon emissions. The larger the building, the more powerful the system required. By adding filters to electricity-driven systems, property owners can ensure optimal energy efficiency, as well as quality air circulation for inhabitants.
System Retrofits
According to the Department of Energy, “system retrofits in commercial buildings are critical to achieving aggressive energy-reduction goals.” Recent research revealed that forty percent of projects with high energy savings were found to include system retrofits, while only 16% of projects with low energy savings included system retrofits.
Numbers don’t lie. Retrofits can and do achieve maximum energy efficiency, particularly in large buildings. Insulation window film, as well as varying solar window films, provide remarkable improvements in the energy efficiency of commercial buildings. 3M™ solar window films were recently accepted into the Green Proving Ground (GPG) program. Once approved, we can expect to see greater implementation of commercial window film use as it is often more cost-effective than replacing glass windows or doors.
Energy Agencies
If you are unfamiliar with the GPG, it is one of several government programs that have been created to ensure carbon neutrality. Under the arm of the Energy Department and the General Services Administration, the GPG program finds and tests energy efficiency innovations. Their system is rigorous and only those solutions that comply with recent standards are approved.
NGS, along with 3M are the latest group approved for GPG testing. The process can take up to a year to complete. Once final tests have been concluded and all expectations have been met, NGS and 3M solar window film will be government approved as a premier energy efficiency solution.
Contracting vehicles have been a part of the federal process for decades. These are government-researched and approved businesses or contractors who provide premier services and fair pricing. NGS is the only film and graphics contracting vehicle in the United States.
As we move closer to carbon neutrality these federal energy agencies will be a “go-to” for both government and commercial building use. These resources will guide the way to our goal of “Carbon zero by 2030.”
Improve Building Energy Efficiency with NGS
As you can see, we’ve gotten serious about carbon neutrality in America. NGS is proud to be affiliated with the elite organizations detailed above. Moreover, we look forward to further aiding our goal of carbon neutrality.
Until we reach the point where we are using exclusively sustainable products, implementing the most energy-efficient and low-embodied materials is a priority. We are all doing the best we can to ensure a carbon-neutral world. Together we can get there – one smart choice at a time.
By applying what we’ve learned and sourcing the best possible choices, we can obtain the “Carbon zero by 2030” target. To learn more about how window films support energy efficiency watch our Improve Energy Efficiency Webinar – NGS Films and Graphics.
Feature image by Viktor Jakovlev